Throughout IDAKA’s 100-year history, no matter what the situation, we have worked closely with our customers to the end, and have been unflinching in our responsibility to deliver. This may seem perfectly natural, but we have built strong relationships of trust with our customers by continuing to deliver what anyone would expect to be natural both reliably and faithfully. 100 years of history speaks volumes about the strength of our relationships of trust.
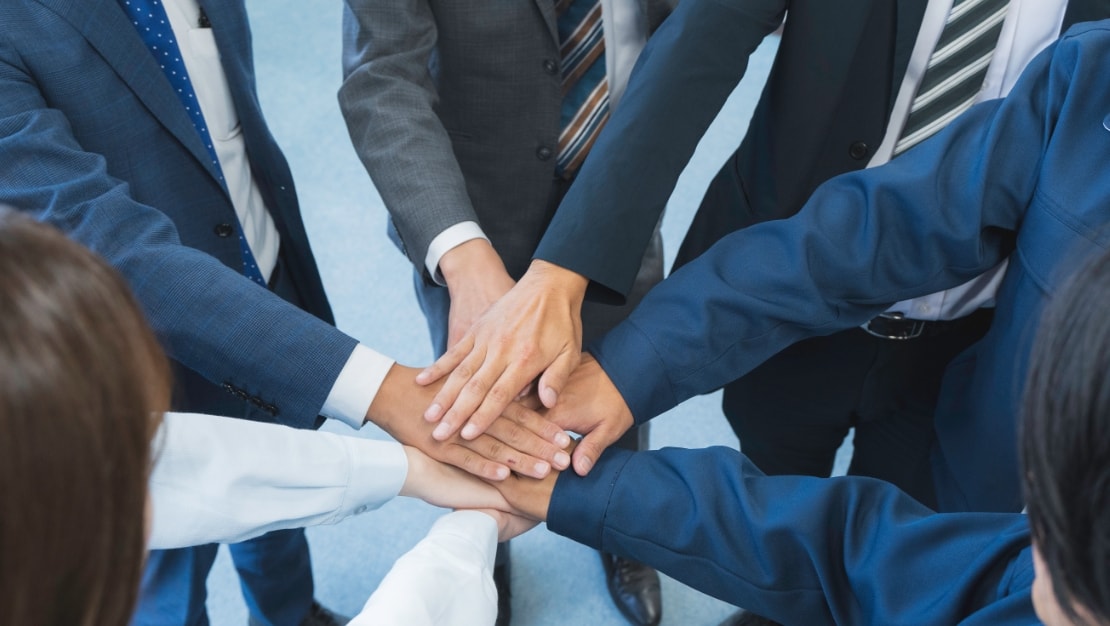
for proposing the optimum solutions
IDAKA deals with approximately 2,800 manufacturers and handles approximately 12 million or more products. This huge selection to choose from ensures that our customers have the very best products to meet their needs. In addition to the product knowledge we get from each manufacturer, we always conduct comparisons of each manufacturer in order to deepen our expertise and allow us to choose the best products on our own initiative. What’s also unique about IDAKA is that we do not belong to the group of any specific manufacturer, allowing us to choose and propose the best products for our customers from a completely objective standpoint.
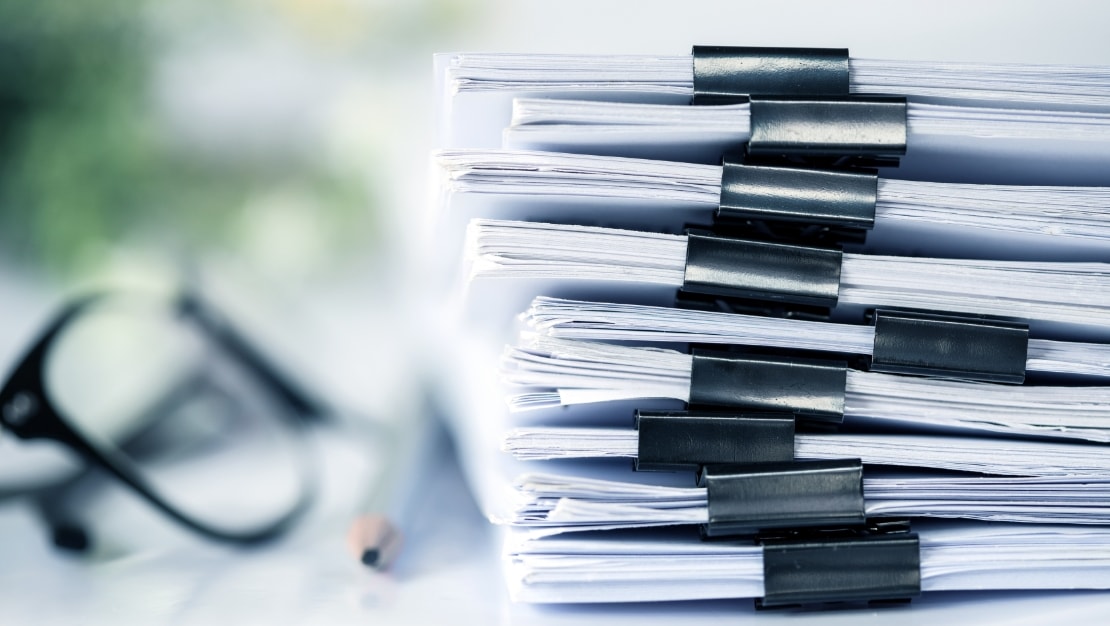
IDAKA values its relationships of trust with our customers. We put together dedicated teams for each customer, and work closely with the customer to address their issues, not only on the individual staff level, but as a team. Moreover, we always assign new employees to work alongside and learn from experienced employees for about 5 years, providing a practical education platform for them to gain knowledge and skills through work experience. 5 years may seem a little long, but we could never let those with insufficient knowledge and experience deal with customers. It is precisely because IDAKA values its relationships of trust with customers that we have maintained our level of accomplishment.
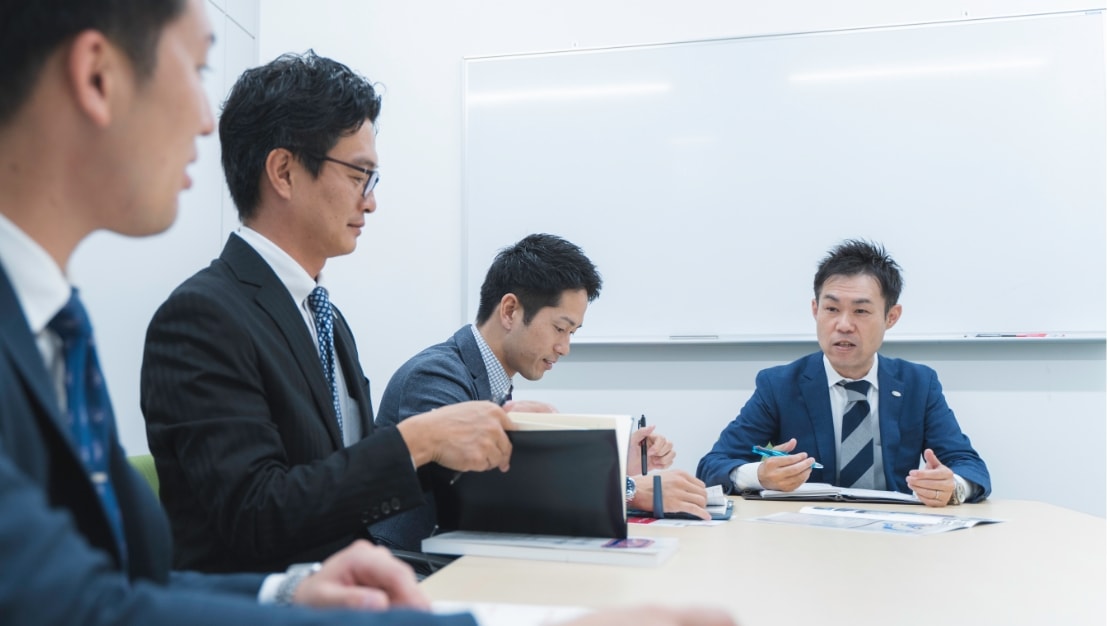
IDAKA is responsible for ensuring that our customers are able to construct their new equipment safely. Naturally, the product manufacturers handle the construction work, but we have established our own “Safety and Health Promotion Department”, who are responsible for patrolling the construction area to ensure that rules are being followed, and that there are no hazardous locations. Moreover, we have also formed the “IDAKA Safety and Health Cooperation” together with our partner companies to raise safety awareness at our affiliates on a daily basis.
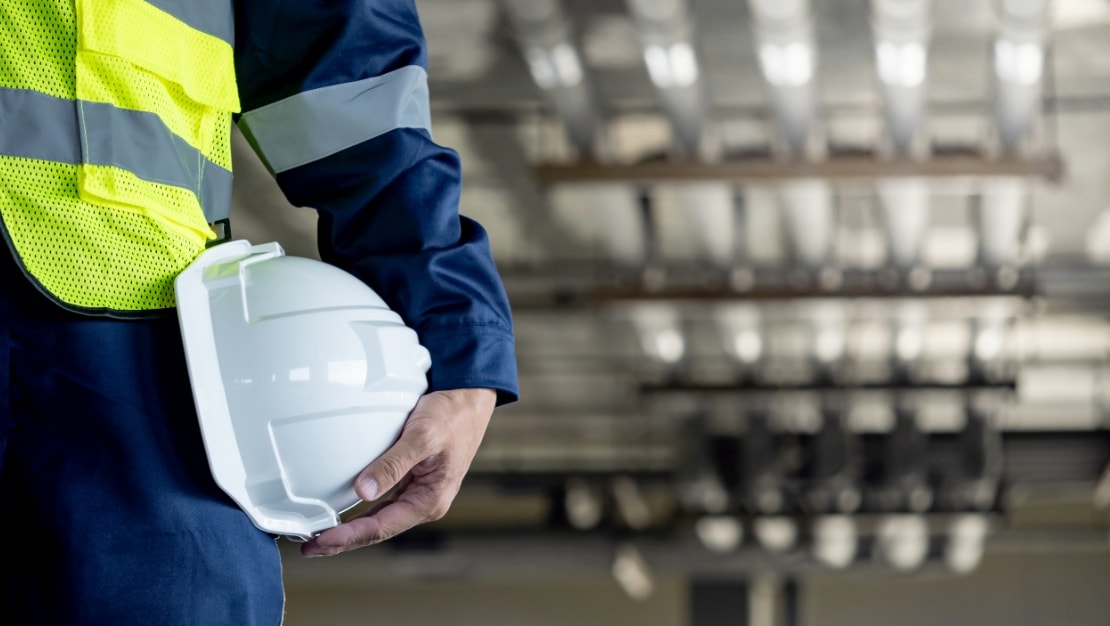
IDAKA provides generous overseas support in the form of help with imports and exports to and from overseas, as well as assistance with part procurement for our overseas customers. We established our own dedicated “Trade Department”, and have put in place an environment in which we can handle all procedures associated with importing and exporting such as customs clearance procedures. IDAKA also has around 20 overseas offices worldwide, allowing us to instantly share know-how cultivated in Japan. This ensures that customers receive the same service regardless of whether they are in Japan or overseas.
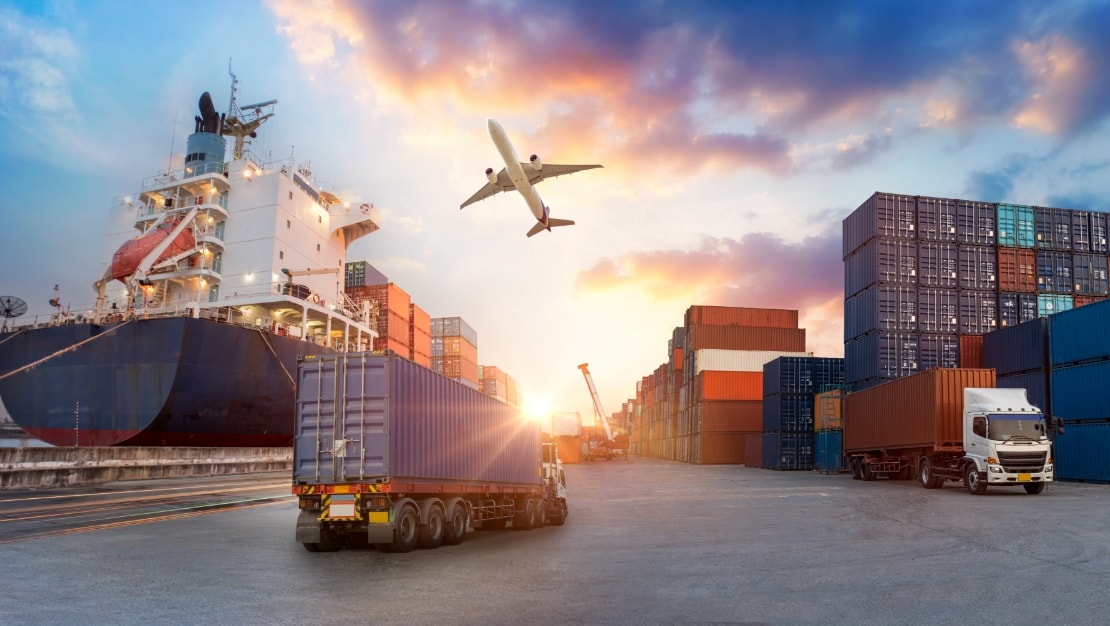
To allow us to propose the optimum solutions to meet our customers’ requirements at all times, we are constantly keeping up to date with new technologies and products, gathering the latest information, and developing relationships with the manufacturers who provide these new technologies. We also carry out development work jointly with manufacturers and customers involving research into potential new fields. In 2018, we established the “Battery Business Promotion Department” to support the promotion of new technologies.
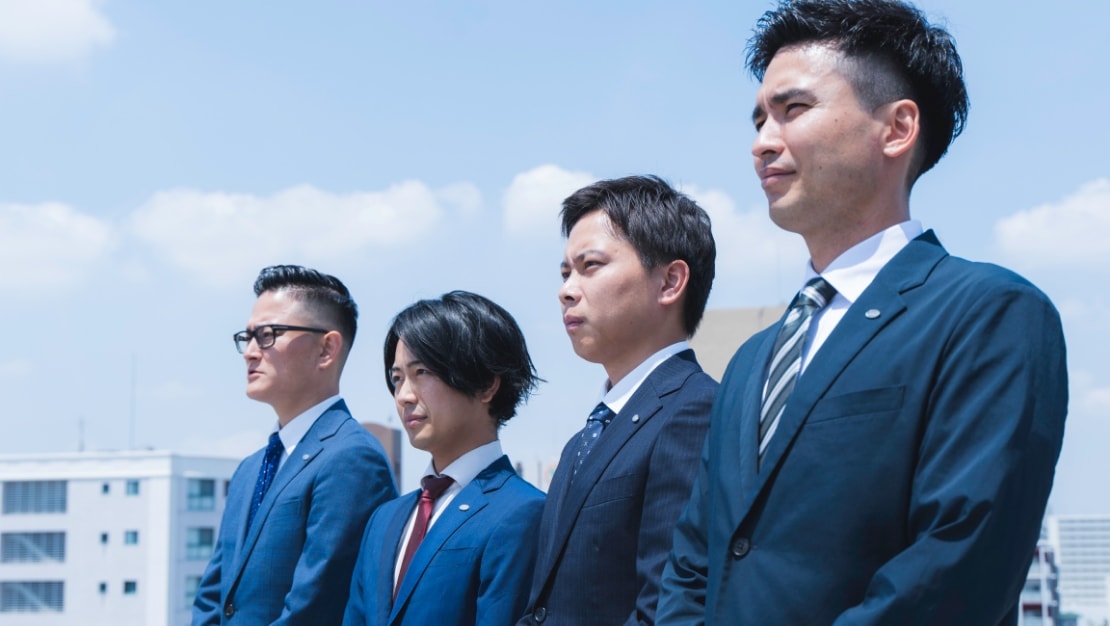
IDAKA aggressively proposes products that are capable of contributing to our customer’s sustainability activities,such as energy-saving products, and products that allow power consumption and CO2 emissions to be visualized.
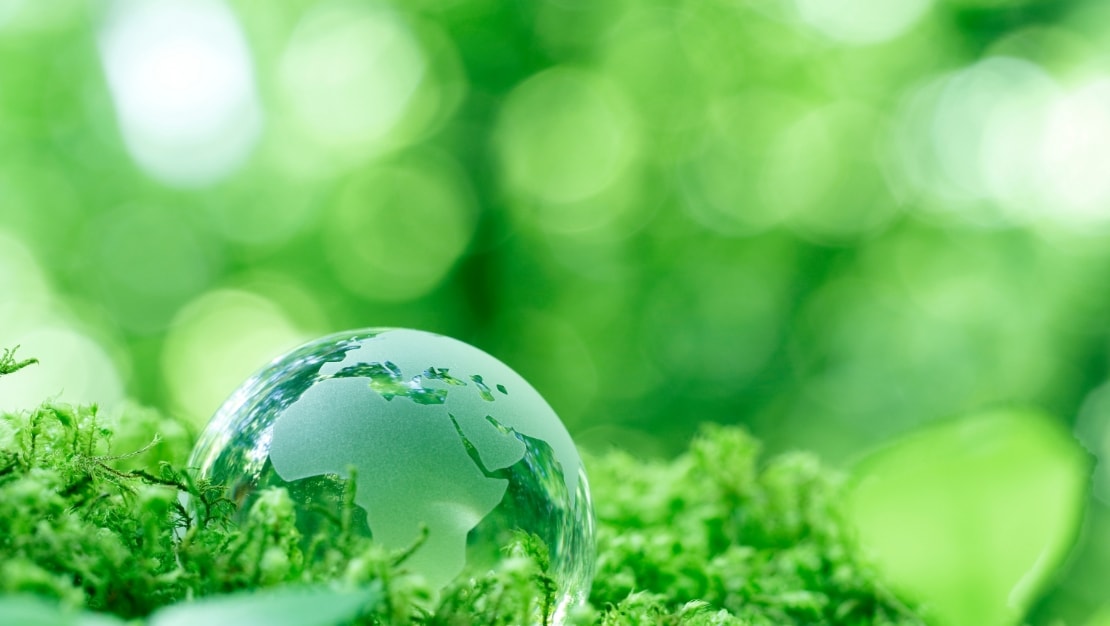
Proposal examples
- We proposed the adoption of an inverter-type compressor. This allowed the appropriate amount of air to be supplied as necessary, contributing to energy saving.
- We proposed the adoption of an oil-free compressor. This allowed clean, oil-free air to be supplied, and eliminated the need for oil replacement, contributing to reduced environmental burden.
- We proposed the adoption of an air leak viewer. Doing so allowed air leaks to be visualized and detected, realizing energy savings by reducing the risk of energy loss.
- By using the latest cutting tools and machining technology, customers were able to realize longer tool life. This contributed to reduced waste for our customers.
- We proposed the adoption of a system that generates power from waste heat and vibrations. This resulted in energy creation at our customers’ factories.